
Since the development of SECS-I (SEMI Equipment Communications Standard 1) in 1980, SEMI has advanced the standardization of semiconductor manufacturing. SECS-I laid the groundwork for communication between equipment and factory systems. Over the years, SEMI expanded its portfolio with SECS-II, GEM (Generic Equipment Model), the GEM300 suite, and the EDA (Equipment Data Acquisition)/Interface A suite, creating a comprehensive framework addressing the industry's diverse and complex needs. These standards provide a common language for communication, data exchange, and control between shop-floor equipment and IT systems. By standardizing these interactions, SEMI has ensured seamless integration across equipment from various vendors, essential for fabs. SEMI standards underpin activities like equipment communication, process control, material management, and data collection.
The evolution from SECS/GEM to EDA
More recently, SEMI introduced Equipment Data Acquisition (EDA), often referred to as Interface A, to expand its standards suite and address the semiconductor industry’s increasingly diverse and complex needs. EDA standards facilitate and streamline communication between a factory’s data collection applications and manufacturing equipment.
The evolution from SECS/GEM to GEM300 and now EDA is a natural progression that reflects the increasing complexity of semiconductor manufacturing. The original SECS/GEM standards established a robust framework for equipment-to-host communication and standardized equipment behavior, enabling reliable interactions and laying the foundation for automation. With the move from 200mm to 300mm wafers, GEM300 was introduced to address higher throughput requirements and advanced process control. Building on SECS/GEM, GEM300 added features such as job management, automated material handling, and material tracking that were critical to support larger wafers and increased production volumes.
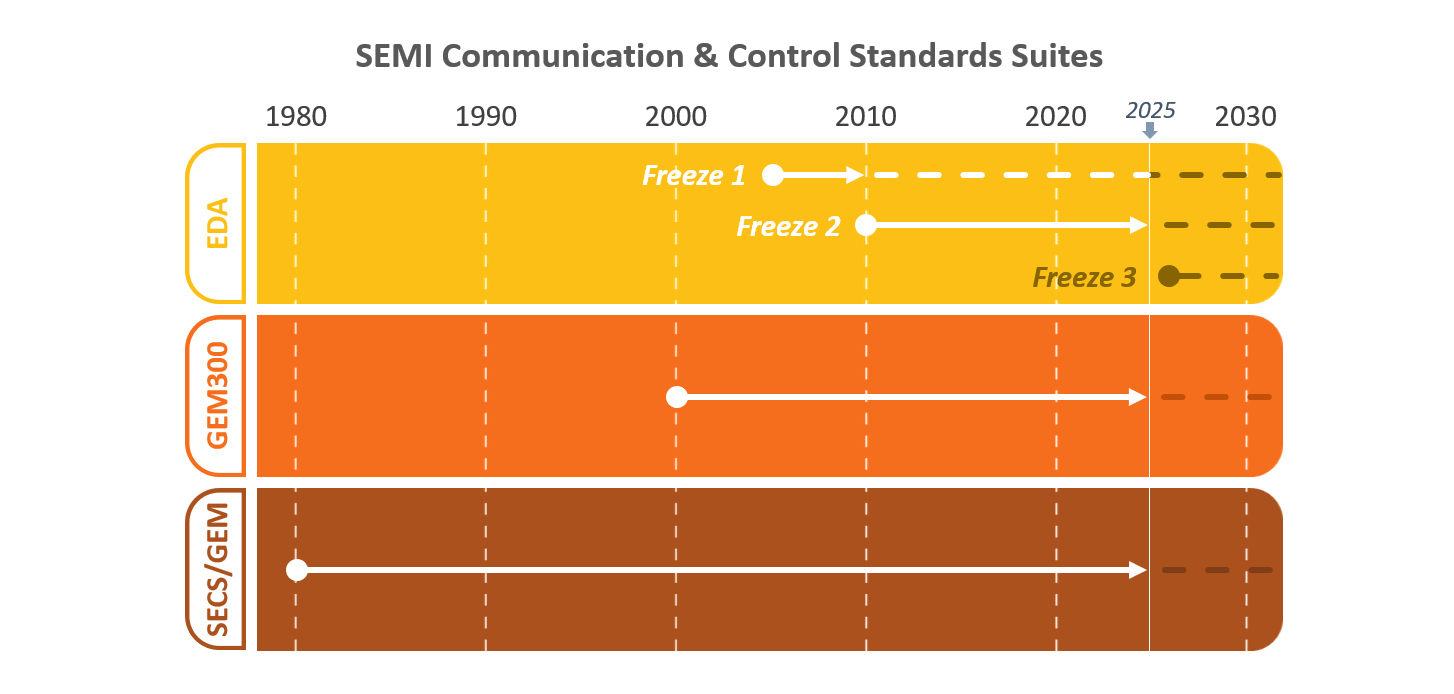
As industry scaled up, the importance of data collection and utilization became paramount. The EDA (Interface A) suite emerged as a solution for high-speed, high-volume data acquisition. Complementing SECS/GEM and GEM300, EDA enables real-time data analysis, process optimization, and predictive maintenance which are vital for data-driven manufacturing.
Together, SECS/GEM, GEM300, and EDA provide a comprehensive roadmap for improving efficiency, yield, and quality control. This evolution ensures that semiconductor fabs remain competitive, highly automated, and ready to innovate in an ever-evolving market.
Leveraging equipment data for fab efficiency
Modern semiconductor equipment generates large volumes of real-time data that underpin a wide range of critical applications, including:
- Run-to-run control (R2R): Dynamically adjusts equipment settings to maintain consistent output quality between production runs.
- Fault detection and classification (FDC): Monitors data to detect and classify anomalies, preventing defects.
- Virtual metrology: Predicts process parameters using sensor data, reducing the need for physical measurements and improving throughput.
- Condition monitoring: Analyses equipment and sensor data to predict and prevent failures, minimizing unexpected downtime.
- Data analysis: Identifies patterns and trends to optimize processes, improve yields, and increase overall efficiency.
These data-driven applications illustrate the transformative impact of harnessing equipment data. By implementing robust data collection standards, fabs can operate with greater agility, solve problems proactively, and continually refine their processes to stay competitive.
EDA Standards
As Moore's Law continues to drive higher transistor densities, semiconductor manufacturing processes have become more complex. The EDA suite provides standardized data structures, formats, and protocols to enable the efficient data exchange between sophisticated equipment and IT systems. Building on earlier SEMI standards, EDA adds capabilities for managing high-speed, high-volume data. Key EDA standards include:
STANDARD | DESCRIPTION |
---|---|
SEMI E120 – Common Equipment Model (CEM) | It provides a unified high-level structure for equipment. |
SEMI E125 – Equipment Self-Description (EqSD) | It standardizes how equipment capabilities and operational states are presented. |
SEMI E128 – Specification for XML Message Structures (Freeze 2 only) |
It defines XML-based message structures for consistent data exchange. |
SEMI E132 – Specification for Equipment Client Authentication and Authorization | It addresses session management and standardizes authentication and authorization for secure data access. |
SEMI E134 – Specification for Data Collection Management | It outlines the process for planning, managing, and executing data collection. |
SEMI E138 – XML Semiconductor Common Components (Freeze 2 only) |
It provides XML components tailored for semiconductor communication. |
SEMI E179 – Protocol Buffers Common Components (Freeze 3 only) |
It specifies a standardized approach to representing errors, data types, data value types, units, and operators through protocol buffers. |
These standards address several critical capabilities such as equipment structure, communication, security, data modeling, and collection planning to enable fabs to gain actionable insights both securely and efficiently.
SEMI E164 bridges EDA and GEM/GEM300 by hierarchically modeling equipment metadata and enabling standardized access to equipment states, regardless of the underlying protocols. This integration ensures seamless data collection from increasingly complex, automated equipment.
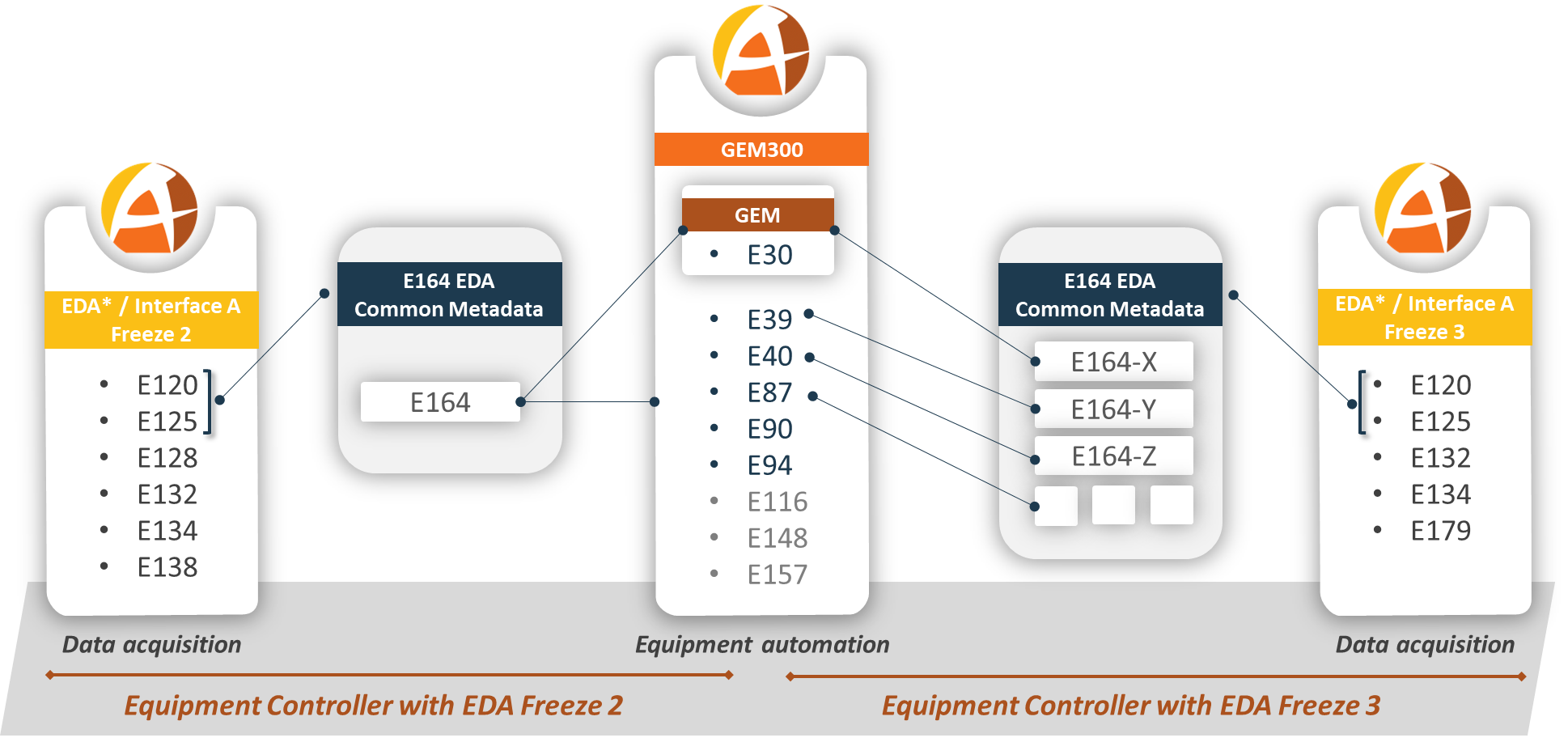
The role of freezes
The concept of a "freeze" stabilizes SEMI standards by designating mature, reliable versions that collectively form the standards suite. SEMI E178 governs freeze versions for EDA, with Freeze 2 serving as the current stable framework for high-speed, high-volume data acquisition. As part of the ongoing evolution, the industry is preparing for Freeze 3, which will introduce support for HTTP/2, gRPC, and protocol buffers, among other enhancements.
A key element of Freeze 3 is SEMI E179, the specification for Protocol Buffers Common Components. This standard establishes a unified approach to representing errors, data types, data value types, units, and operators through protocol buffers. It will replace SEMI E138 and SEMI E128 in Freeze 3, moving the industry from XML-based structures to next-generation data exchange formats.
While Freeze 3 continues to evolve, SEMI EDA Freeze 2 remains a reliable, proven standard that drives data acquisition and integration in today's semiconductor manufacturing. This evolution underscores the industry's commitment to embracing cutting-edge technologies for data-driven semiconductor manufacturing.
With each new process node and the growing adoption of advanced packaging techniques, the global semiconductor industry faces a steep increase in data complexity. With the upcoming Freeze 3 enhancements such as HTTP/2, gRPC, and protocol buffers, SEMI EDA standards are positioned to more efficiently handle these increasing data demands. By improving data throughput and seamlessly integrating with modern analytics and artificial intelligence-driven solutions, these standards enable real-time process optimization, predictive maintenance, and more adaptive manufacturing operations. Fabs that embrace this evolution will realize superior yields, faster innovation cycles, and a sustainable competitive advantage in an ever-accelerating market.
Why Agileo is your partner of choice for your EDA transition
Agileo has carried out EDA Freeze 2 client and server tests with equipment manufacturers already supporting EDA and is working with these early adopters on the integration on their equipment using A²ECF-SEMI, Agil'GEM, and Agil'GEM300. We will soon be providing a comprehensive offer for OEMs in need of EDA Freeze 2 or 3. Agileo is a major contributor to that global effort and pleased to support OEMs in all market segments with a complete and scalable product suite to enable production facilities to embrace this evolution to realize superior yields, faster innovation cycles, and a sustainable competitive advantage in an ever-accelerating market. We invite you to contact us to discuss your specific EDA needs in more detail.